Proper storage of necessary components can help the upstream and downstream of the industrial chain to cope with the supply crisis
Whether the storage and handling of electronic components are standardized and correct is one of the criteria to distinguish the advantages and disadvantages of component distributors. On the one hand, the upstream original factory will list the 'component storage specification' as a part of the evaluation criteria for authorized partners; On the other hand, standardizing the storage mode of electronic components is a key link for distributors to practice product quality management. Incorrect storage mode will lead to damage or even scrap of components.
Therefore, when dealing with the storage problems related to electronic components, enterprise decision-makers must have a problem-solving mentality. This means that enterprises need to invest more resources, such as using climate control systems, building automated warehouses, and so on.
Understand the risk of component storage failure
The nonstandard storage mode of electronic components will have many negative effects. First of all, understanding the risks that may arise from the storage of components can prompt warehouse managers to formulate appropriate preventive measures in advance, so that they can be more familiar with solutions and avoid them.
During storage, oxidation and vapor diffusion are two major risks faced by electronic components.
Generally speaking, the oxidation rate of articles in an ultra dry environment will become slow. Therefore, storing electronic components in a dry storage cabinet is a solution to prevent oxidation. Another solution is to put the components in a vacuum packed moisture-proof bag. As long as the bag is filled with nitrogen, it is an absolutely feasible anti-oxidation method.
Similarly, dry storage cabinets and moisture-proof bags can also effectively prevent components from absorbing moisture or gas.
Vapor diffusion refers to the way steam moves with air flow or pressure difference. In the component warehouse, the steam may spread to various places, especially the printed circuit board (PCB) and other precision components, which have a high risk of absorbing moisture. Therefore, putting the components into the moisture-proof bag and storing them in the dry storage cabinet can reduce the threat of steam diffusion.
The third storage dilemma of electronic components is difficult to visualize. Without disassembly, it is usually impossible to find the damage degree of the components themselves.
What are the new changes in the distributor's inventory strategy? From November 10 to 11, the second stop of the International IC&Component Exhibition and Conference (IIC for short) will be opened in Shenzhen, a global innovation center. At the same time, there will be a global CEO summit, a global distribution and supply chain leaders summit and several theme forums. Click here or scan the QR code to register for the conference for free! Discuss the trend of electronic industry and technology with Shenzhen high-quality distributors, and seize new opportunities in the distribution market!
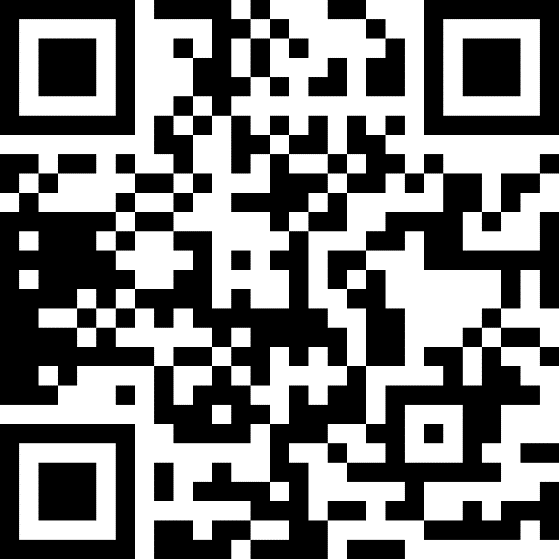
Cooperate with temperature and humidity control system supplier
The 'climate control system' of the electronic component warehouse mainly controls the two factors of temperature and humidity, so it can also be directly called the 'temperature and humidity control system'. The temperature and humidity control system supplier is proficient in the anti oxidation and moisture-proof methods of warehouse storage, and can put forward professional storage specifications for different types of components.
Keeping constant temperature and humidity in the warehouse is crucial to the storage of electronic components. The temperature will change the shape of the plastic, and the metal will expand or contract due to the temperature change. Humidity is also critical. When the humidity is too low, the resistance of components will be reduced and the components will become brittle; On the contrary, excessive humidity will have a negative impact on the conductivity of components.
At present, most of the suppliers who provide temperature and humidity control systems will adopt a variety of ways to protect the climate environment of the warehouse.
One is to set up special temperature zones for different types of components, or use seals around the doors to reduce climate change caused by frequent personnel access. The other is the use of IoT temperature sensors, which can help warehouse managers verify whether the climate conditions meet expectations in real time. In addition, having a backup climate control system is essential for contingency planning.
Help from Automated Warehouse
At present, more and more leading distributors in the industry spontaneously pursue automation to improve their work processes. These automation attempts are not only reflected in warehouses, but also in production and manufacturing, internal management, and strategic decision-making.
As mentioned above, it is a reliable way to put electronic components in a storage cabinet with constant temperature and humidity. On this basis, many factories further deploy automation to improve the operability of this method. For example, add automatic transportation tools to reduce the actual contact times between components and personnel when moving in the factory.
Take Digi Key as an example. He is a small batch and multi variety component distributor. Recently, he opened a new factory in Minnesota. This 2.2 million square foot distribution center is almost completely automated. More specifically, part picking is the only work that needs to be done manually. The factory has more than 27 miles of automatic conveyor belts. On average, a component order will move more than 3200 feet inside the factory, and finally reach different destinations.
Automation leaves most of the work to intelligent systems, which are not as distracted or tired as humans. This is the fundamental reason why manufacturers use automated processing of printed circuit boards and automated storage solutions. If the automation system places the components in the correct position, the possibility of errors will be reduced. In addition, well adjusted automation systems are usually more efficient than people.
Summary
If enterprise decision-makers do not fully understand and solve these problems, electronic component storage problems will inevitably affect product quality, and even lead to customer dissatisfaction. This means that whether it is to use temperature and humidity control systems, pursue automation, or research new strategies, enterprises must take action quickly and proactively, rather than running at the risk of damaging components.
In addition, many electronic components are in high demand and short supply. Proper storage of necessary components can help the upstream and downstream of the industrial chain to cope with the supply crisis and ensure that there are more available components to ensure normal production and operation.
The article is translated from EPSNews, a sister magazine of International Electronic Commerce, with the original link:How to Avoid Electronic Component Storage Woes